Electric motors now form an important component of all industries, modes of transport or even within kitchen appliances which most people use. The ability of motors to change electrical energy into mechanical energy has seen the rise of their usage in different fields. Understanding the Types of Electric Motors is important especially now that there is a shift towards more environmentally and energy-friendly means. This detailed article will define Types of Electric Motors, their usage, advantages, and limitations to assist you in making the right choice on the motor you need.
What Is an Electric Motor?
A Types of electric motors is a type of device that accomplishes the conversion of electrical energy into mechanical energy because of the presence of magnet interaction and the current-carrying wires. In most cases, electric motors consist of three main parts which are the rotor, stator and the electric current source which supplies required electric power. They vary with respect to size and type depending on their use, structure and the working principle of the types of electric motors.
Types of Electric Motors
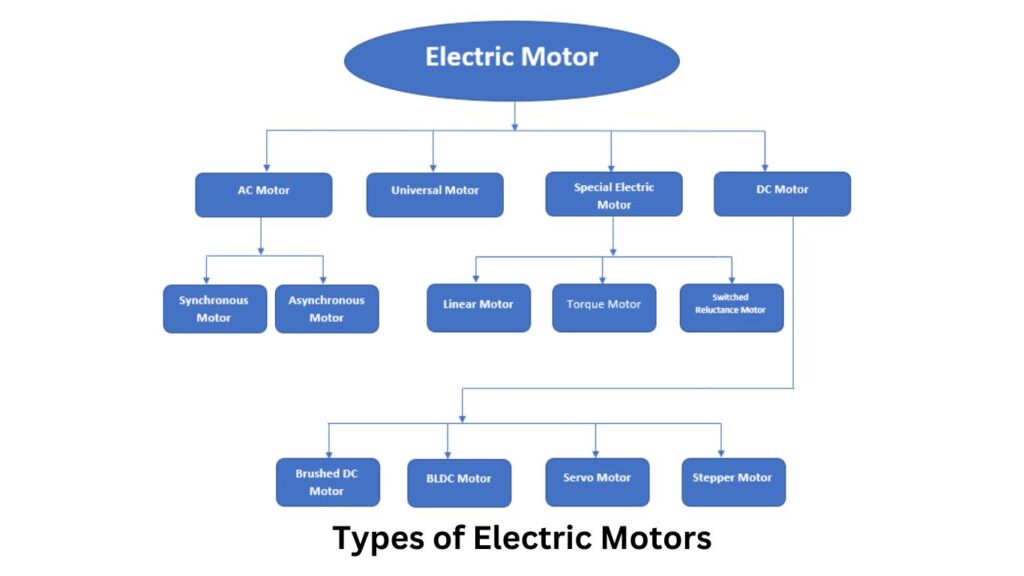
In general terms, Types of Electric Motors define into two major categories.
- AC Motors (Alternating Current Motors)
- DC Motors (Direct Current Motors)
Both AC and DC motors have subcategories, each designed for specific purposes and operational characteristics.
1. AC Motors
The alternating current during the operation of AC motors always changes its direction. These AC motors are found in many applications including industrial, domestic and home HVAC applications. AC motors can be further broken to two major types:
1.1 Synchronous Motors
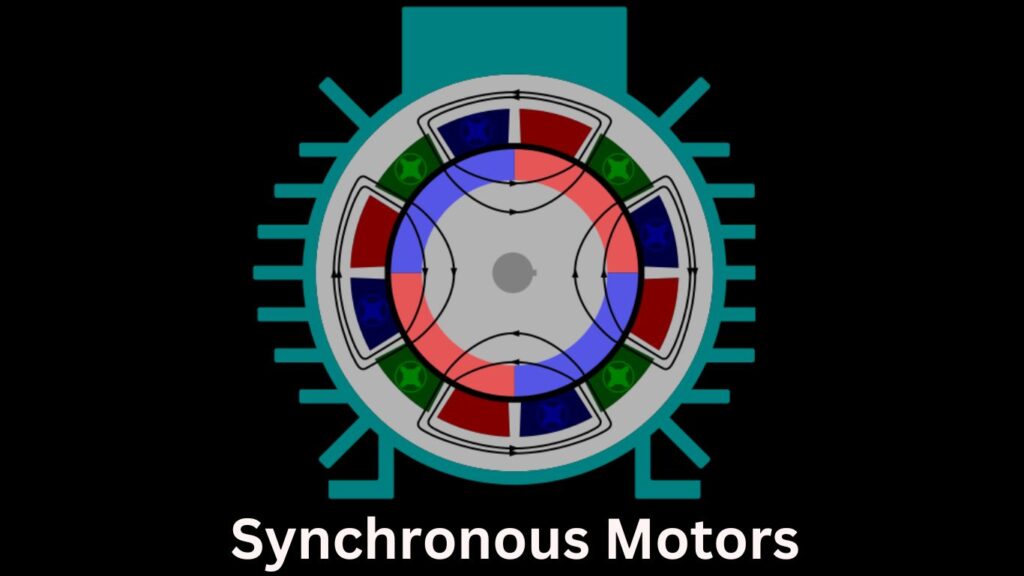
Synchronous motors are a types of electric motors that operates at a constant speed that is in direct ratio with the supply frequency. In these poles, the rotor speed is synchronized with the frequency cycle of the AC power supply. Synchronous motors are widely used in applications where speed control is a major issue such as in conveyors, robots and even some machinery.
Advantages:
• High levels of effectiveness.
• Great management of speed and location.
• High power demand applications are feasible.
Disadvantages:
• Other devices such as slip rings and brushes are needed in order to initiate motion.
• Initial costs are very high.
1.2 Induction Motors (Asynchronous Motors)
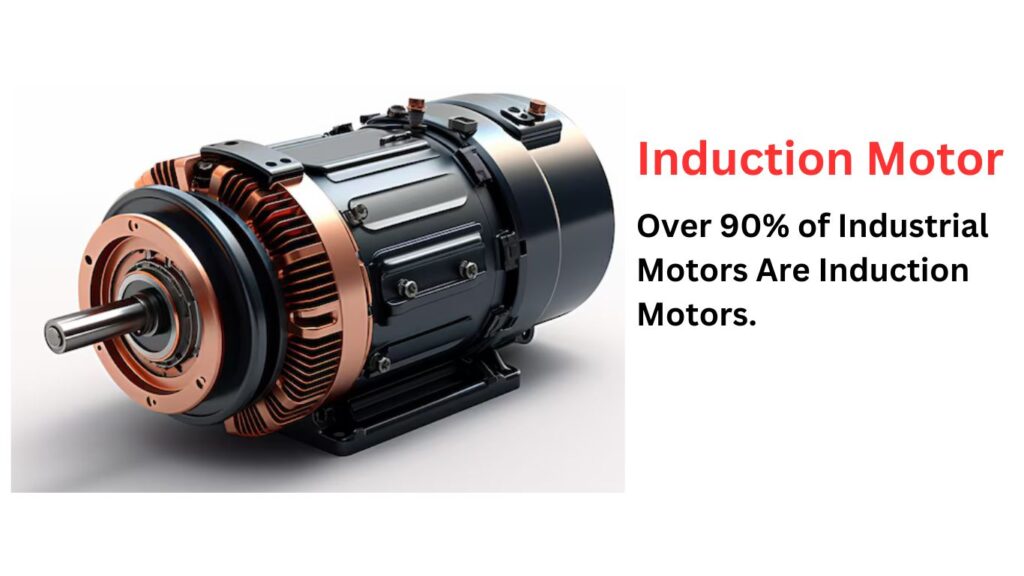
The polyphase induction motor is the most widely used member of the ac motors group and its working principle is its basic because it is over driven and does not necessarily follow the electrical field. The frequency slip (frequency difference between power supply and motor speed) exists in case of upset loads. These can be further distinguished into:
1.2.1 Single-phase induction motors:
A single-phase induction motor is an types of electric motors that operates on single-phase alternating current (AC). These motors are widely used in household appliances, small machinery, and other low-power applications where three-phase power isn’t available.
Working Principle:
The operation of a single-phase induction motor is based on the principle of electromagnetic induction. When a single-phase AC voltage is applied, it creates an alternating magnetic field. However, a single-phase induction motor is not self-starting because the magnetic field produced is not rotating but pulsating. To achieve starting, an auxiliary mechanism or additional circuitry is required to create a rotating magnetic field.
1.2.2 Three-phase induction motors:
A three-phase induction motor is a self-starting motor that operates on a three-phase alternating current (AC) supply. These motors are the most commonly used in industrial and commercial applications due to their reliability, efficiency, and simplicity.
They are widely used in industrial workplaces owing to their sturdiness, dependability, and efficiency.
Working Principle
The operation of a three-phase induction motor is based on Faraday’s Law of Electromagnetic Induction. When a three-phase AC supply is fed to the stator windings, it creates a rotating magnetic field (RMF). This RMF induces an electromotive force (EMF) in the rotor due to relative motion, generating a current in the rotor conductors. The interaction of this current with the RMF produces torque, causing the rotor to rotate.
Advantages:
• Simplified and strong styling.
• Little upkeep.
• Peace of mind.
Disadvantages:
• Achieve less response to speed adjustment.
• Less effective than a synchronous motor.
2. DC Motors
A direct current is used to operate a device known as a DC motor, which is famous for speed and torque control. It is readily seen in systems where speed varies like in electrical transport, robotics, and small equipment. DC motors are further subdivided as follows:
2.1 Brushed DC Motors
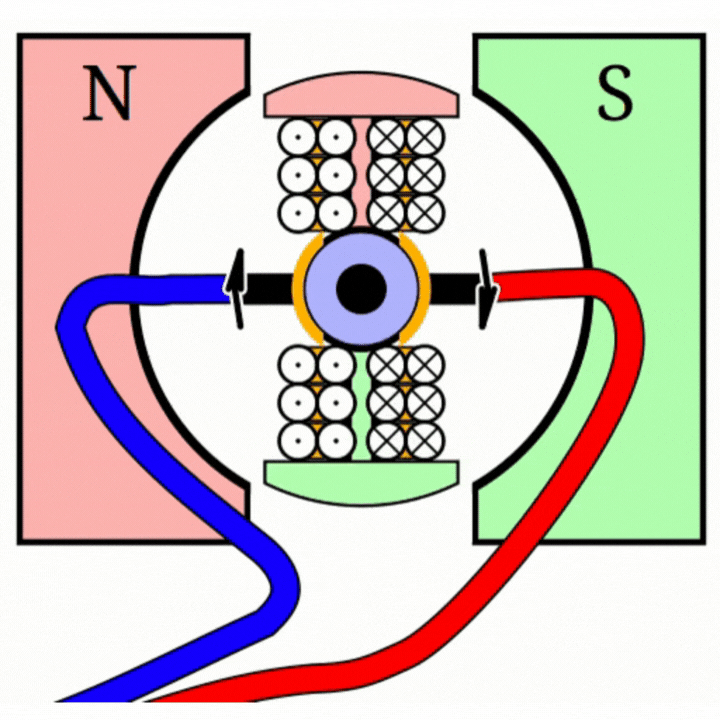
Brushed or simply brushed DC motors are the simplest classification of the DC motor system. In this type, brushes and a commutator are used to direct current to the rotor windings through an electromagnet. This types of electric motors is common in toys, automotive starter motors or small appliances.
Advantages:
• Easy to design and efficient to control.
• Cheap and effectively used in small applications.
• Very good low speed torque.
Disadvantages:
• High maintenance due to the blades brush wear.
• Brushes have a short working life.
2.2 Brushless DC Motors (BLDC Motors)
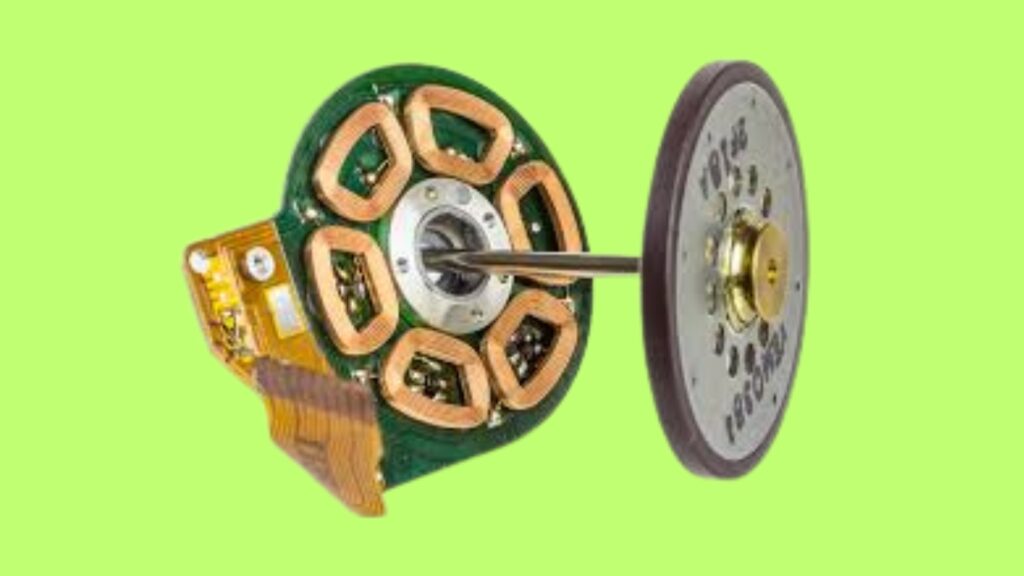
Brushless DC motors are capable of doing away with a commutator and brushes since their controls are operated electronically. Compared to the brushed motors, these types of electric motors are more efficient and therefore have an extended service life. These types of electric motors are used for such applications as drones, electrical vehicles and computer cooling fans.
Advantages:
• High efficiency with long lasting lifespan.
• Minimal servicing.
• Good enough speed and torque.
Disadvantages:
• Higher initial price.
• Complicated control systems.
2.3 Servo Motors
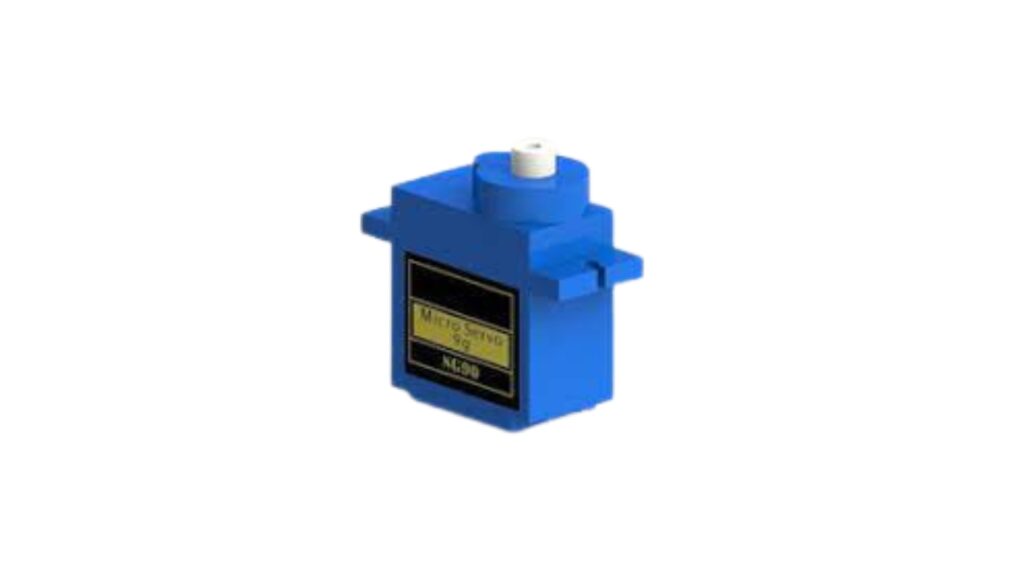
A servomotor is a special rotor – armature-fed DC motor that has embedded circuitry and is manufactured for the purpose of controlling movement with respect to distance, angular position, linear position or motion derivative such as velocity or acceleration or its second derivative, which is called jerks. Control devices of this type are used in Marking, welding machines, robots and automated manufacturing facilities where motion should be performed with high precision.
Advantages:
• Very good in position control.
• Very simple to operate.
• Very efficient.
Disadvantages:
• Around stalling conditions, excessive torque cannot be relied upon.
• It is costly as compared to standard types of motors.
2.4 Stepper Motors
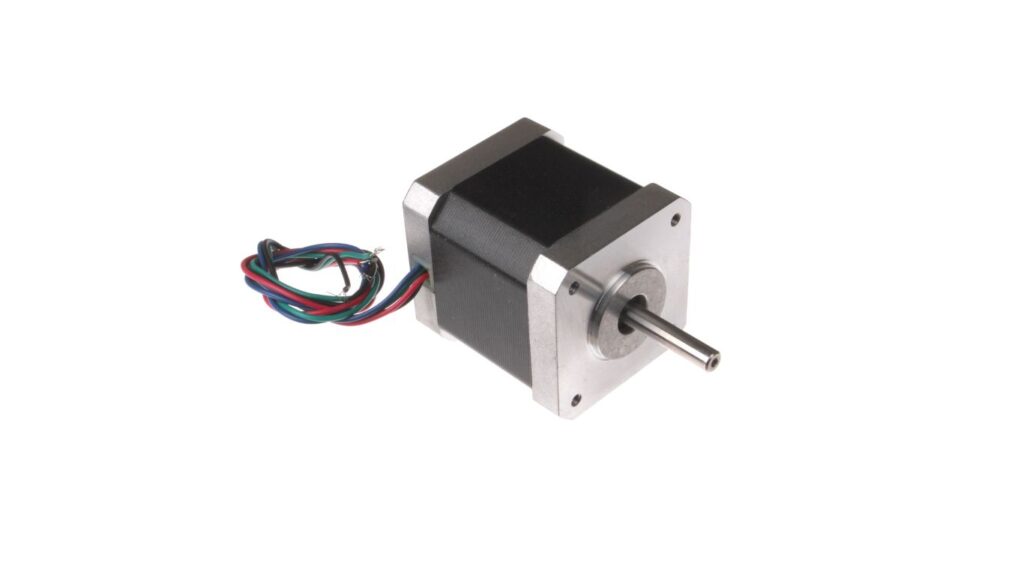
Stepper motors are made in such a way that they would achieve rotation in a number of steps over a given degree of movement increasing thus control of a stepper movement. Stepper motors are used in 3D printer, CNC cutter and in cameras in order to achieve smooth steps.
Advantages:
• There is no need of feedback in order to achieve errorless positioning.
• Direct control is quite easy.
• Cheap days for common designs.
Disadvantages:
• They offer weak torque, especially when operating at high speeds.
• They might have concerns with resonance.
3. Universal Motors
A universal motor is a very versatile motor that operates on both alternating current and direct current. It is used primarily in high speed applications such as power tools, vacuum cleaners and kitchen devices. The reason why constant speed fan type universal motor is used very often is the combination of small size and high specific power.
Advantages:
• High operational speeds and good power output.
• Small and light weight.
• Both AC and DC power sources can be used.
Disadvantages:
• High heat, noise and vibration.
• The service life is shorter when compared to other motors.
4. Special Types of Electric Motors
In addition to the widely known AC or DC motors, there are several specific types of electric motors that are made for special applications. These are known as special-purpose electric motors, and they possess features that make them suitable for application in specific niche markets.
4.1 Linear Motors
This types of electric motors does not produce rotational motion but rather thrust motion, linear motion to be precise, tools that possess this motor configuration are used in places where quick motion is desired and not rotational motion. Linear motors can also find applications in magnetic levitation SHL trains, conveyor systems, and precision machines.
Advantages:
• Linear motion is completed at high speed.
• No moving parts thus no mechanical transmission systems required.
• Smooth and accurate control of movement.
Disadvantages:
• The design is complex and also expensive.
• Has a small degree of freedom in motion.
4.2 Torque Motors
Perfectly suitable for low-speed applications, torque motors are direct-drive motion devices which are meant for use delivering high output torque at low RPM. Typical applications include wind turbine power units, automotive steering systems, and industrial automation.
Advantages:
• Output torque is very high.
• Avoidance of mechanical transmission components.
• Smaller construction.
Disadvantages:
• speed range is restricted.
• It is more expensive as compared to standard engines.
4.3 Switched Reluctance Motors
Switched reluctant motor is one such new type of motor that works through changing the reluctance in the magnetic circuit. In quest for high power, speed and efficiency, these motors are known to have simple structures. Hence it’s possible to use them in electric motors and industrial machines as well.
Advantages:
• High speed and efficiency.
• Strong and uncomplicated construction.
• Low wear parts.
Disadvantages:
• High vibration and noise levels.
• Difficult control mechanisms.
The Types of Electric Motors Symbols :
Types of Electric Motors | Symbolic Representation |
Generic Motor | ![]() |
Dual Speed Motor | ![]() |
AC Motor | ![]() |
DC Motor | ![]() |
Linear Motor | ![]() |
Stepper Motor | ![]() |
Electrical Machine | ![]() |
Permanent Magnet DC Motor | ![]() |
AC Single Phase Series Motor | ![]() |
DC Series Motor | ![]() |
Ac Single Phase Induction Motor with Winding Terminals brought out | ![]() |
Single Phase Repulsion Motor | ![]() |
DC Shunt Motor | ![]() |
Single Phase Synchronous Motor | ![]() |
DC Compound Excitation Motor | ![]() |
3 Phase AC Motor | ![]() |
3 Phase Star Shaped Motor | ![]() |
3 Phase Wound Rotor Motor | ![]() |
3 Phase Linear Motor | ![]() |
Practical Applications of Different Types of Electric Motors
Industrial machine
Laths, Hitch and grinders for the processes of manufacturing and machining in general.
Transport
With the use of electric vehicles, trains and Conveyors which facilitate the movement of goods and humans.
Pumps and Compressors
Industrial water pumps including irrigation systems and hvac compressors.
Domestic Appliances
Fans, washing machines, refrigerators which help in daily activities.
HVAC Systems
Includes air conditioning, ventilation systems and heat systems in construction.
Robotics and Automation
Includes Robots, conveyor systems and pick-and-place machinery for intricate tasks.
Renewable energy
Wind turbines along with solar tracking systems to generate clean energy.
Efficiency of Different Types of Electric Motors
The Efficiency of Different Types of Electric Motors depends on its design and use. So, let’s put it briefly:
AC Induction Motors are rated 85–95% efficiency and work well under steady conditions which fits industrial applications like pumps and conveyors. On the downside, when the load goes down, the efficiency also degrades, and speed control would mean using VFDs.
DC motors brushless ones (BLDC) work on 85–98% efficiency which is an acceptable range with almost no energy loss so it is quite reliable. However, this motors are expensive, the cheaper variant has kind of a brush but drones and electric cars prefer these ones.
A brushed DC Motor would be between 75 and 80 percent efficiency. This types of electric Motors are cheap and easy to use, hence they are ideal for from toys to portable tools but the brushes wear out pretty easily so frequent maintenance is needed.
Synchronous Motors are useful in industries because they have an outstanding 90 to 99% efficiency and work best when operated at a constant speed, This types of electric Motors are also useful to power correction systems.
Knowing these figures is useful when trying to determine which will be the best motor in terms of cost and power savings.
Key Factors to Consider When Choosing an Electric Motor
When you want to use an electric motor for a given application, there are several factors that you need to bear in mind:
Power Requirements:
You will need to identify voltage, current and power for the application. For high power applications, industrial engines like three phase induction motors might be required but in small devices simple brushed dc motors are suitable for use.
Speed and Torque:
The types of electric motors vary in the areas of speed control as done by for example synchronous motors while in other types such as torque motors torque is emphasized. You should pick the type of motor that complies with your desired parameters on speed and torque.
Efficiency:
The operation of high efficiency motors such as brushless DC motors or synchronous motors is beneficial in that operational costs can be cut down which improves the environmental agenda.
Maintenance:
Electrical motors, for instance brushed DC motors, will often need a lot of maintenance because of how fast the brushes wear out. This is not an issue with brushless and induction motors as they tend to be maintenance free.
Environmental Conditions:
Ask yourself if the motor is to perform in recessed or rugged situations such as very high temperatures, moisture or dust factors and thus select suitable motors that possess the right protection, and being tough/ durable.
The Future of Electric Motors
Electric motor technology keeps evolving as industries gravitate towards energy efficiency and sustainability. Current trends such as smart motors interfacing with IOT devices and the introduction of new materials to optimize efficiency in motors and the upsurge in demand for electric vehicles has triggered advancements in motor designs.
For their efficiency and effectiveness in electric vehicle applications, switched reluctance motors and permanent magnet motors are on the increase. In a similar way, the application of types of electric motors in renewable energy system such as wind turbines and solar electric machines continues to challenge innovation.
Conclusion
Different types of Electric motors are an everyday reality whether it is in the line of industrial equipment or in the case of home appliances. Therefore, in choosing the appropriate electric motor, it is useful to know the different types of electric motors such as AF or DC, brushed or brushless, and synchronous or asynchronous ones.
FAQs (People Also Ask About Types of Electric Motors)
Q1. What are the main variations between AC and DC motors?
An AC motor’s electrical energy input source is A/C, and it is generally deployed where a constant rotating speed with consistent effectiveness is needed e.g. in industrial equipment, HVAC systems etc, while a DC motor draws its electrical energy from the Direct Current which has the advantage of better control and high starting torque. This makes it ideal for producing variable speeds which are required in electric vehicles and the robotics industry.
Q2. What is the most effective Electric Vehicle motor?
As the phrase goes, “electric cars’ motors for love”, the most suitable motors for electric vehicles are the Brushless DC motors (BLDC) and AC induction motors. All thanks to their high efficiency, compact size and exceptional control precision, BLDC motors are difficult to outdo. Another plus for high-powered electric vehicles would be the use of AC induction motors due to their robustness and excellent torque capabilities.
Q3. What is a significant improvement achieved by employing a brushless motor?
Motors of this category have several advantages over conventional appliances, including the loss of electrical and friction related losses caused by brushes; Dry low friction motors are effective in eliminating that issue. They are more efficient and trustworthy, need less maintenance, and last much longer than their counterparts. They are quieter as well which makes them perfect for use in quiet electric vehicles or drones.
Q4. What is a stepper motor, how does it work and where is it utilized?
A stepper motor is a types of electric motors that moves in distinct steps, thus providing control and positioning of a rotating shaft. This feature allows it to be widely used in applications such as 3D printers, CNC machines, medical equipment, and robots which require accurate and repeatable motion in the same position.
Q5. Where do the two types of motors differ, that is, a synchronous motor and an induction motor?
A synchronous motor rotates at a speed which is constant and in accord with the AC supply frequency, thus it is ideal for applications where the speed needs to be constant and accurate like a power factor correction. In contrast, the induction motor operates by having the rotor lag slightly behind the rotating magnetic field of the stator, with industrial equipment being its primary application thanks to its straightforward and strong design.
Q6. Can electric motors be deployed in regenerative braking systems?
Yes, it is possible to utilize electric motors in regenerative braking technology, most especially for all-electric vehicles and hybrid electric vehicles. This system captures the kinetic energy produced by the vehicle during the slowing-down process, generates electricity which is packed in the battery, thereby enhancing energy efficiency and increasing the distance the vehicle can cover.
Visit our latest Blog about (Transformer Protection Basics: Everything You Need to Know). Any question regarding Types of Electric Motors & How to make a Difference? please contact us.